将增材搅拌摩擦沉积AFSD纳入混合制造工艺 - 知乎
作者:托尼·施密茨---田纳西大学诺克斯维尔分校教授 | 橡树岭国家实验室联合教授
混合制造结合了增材制造(AM)来沉积预成型件、计量学来确定打印预成型件的几何形状以及CNC加工来获得最终零件的几何形状、表面光洁度和公差。
混合制造工艺规划可包括七个关键步骤:
1. 数字化零件设计
2. AM工艺的路径规划
3. 使用增材制造金属沉积来生产预成型件
4. 测量预成型件以确定其几何形状,并使用可用(例如,构建板的边缘)或添加的(例如,工具球)特征或基准来识别其坐标系
5. 通过导入测量的预制件几何形状并将其用作具有预定义坐标系的毛坯模型来进行CNC加工的路径规划
6. 使用基准点建立的坐标系对预成型件进行CNC加工,使其达到设计尺寸和表面光洁度
7. 测量加工零件以确保符合设计意图。
一种新的增材制造工艺是增材搅拌摩擦沉积 (AFSD)。AFSD是一种固态增材制造工艺,为基于光束的增材制造工艺提供了替代方案,该工艺可局部熔化材料以获得所需的近净形状几何形状。AFSD通过方形截面延展性金属合金原料的塑性(永久)变形来实现固态沉积。包含方孔的工具主轴组件在原料通过主轴轴向进给并靠着构建板或之前的层旋转时对原料进行限制。主轴旋转通过沉积物和构建表面之间的摩擦产生热量,从而减少材料流动所需的应力。在工具以选定的工具进给速度沿着规定的运动路径运动期间沉积原料。还指定了通过刀具主轴的原料进给速度。组合的工具旋转和进给运动使各层能够粘合到构建板和先前的层上,以沉积所需的预成型件几何形状;参见封面图 1。:AFSD,其中原料以逐层方式沉积以获得金属预成型件。照片来源:托尼·施密茨
为了演示使用AFSD、结构光扫描(用于测量预成型件几何形状)和CNC加工的混合制造,选择了六角圆柱体几何形状并生产了演示零件。AFSD使用MELD Manufacturing L3机器完成。如图1所示,使用位于主轴上方的螺杆式致动器迫使9.5毫米方形金属原料通过旋转主轴。
执行器使0.5米长的原料能够随主轴旋转,同时提供轴向力和针对构建板或前一层的材料进给。打印材料受到旋转工具和打印平台板/前一层之间的间隙(1毫米至3毫米)的轴向约束。铣削是使用Haas VF-4三轴数控铣床完成的。车削是使用Haas ST-15数控车床完成的。使用ZEISS/GOM ATOS Q进行结构光扫描。
六角柱加工顺序包括双面6061铝沉积和间歇加工方法。首先将六边形沉积在25毫米厚的方形6061铝构建板上。原点设置在构建板顶角处,用于螺旋插补工具路径,以使用2毫米层高生成六边形形状。
在L3机器上,使用主轴和寻边器在打印平台顶角处设置工作坐标系。然后在构建板的顶面上进行沉积,使用四个趾夹(每个角各一个)将其夹在机器工作台上。使用300 RPM的主轴速度、139.7毫米/分钟的材料进给速率和132.1毫米/分钟的工具进给速率来沉积初始层。随后的各层以160 RPM的速度以相同的进给速率沉积。
沉积后,扫描六边形预成型件和构建板。图2(a)显示了沉积的六边形。然后使用构建板底角处的原点对齐零件设计和预成型件,并通过CAM软件生成铣削刀具路径,并将导入的扫描用作毛坯模型;参见图2(b)。将构建板夹紧在CNC铣床工作台上的一对预先对准的虎钳中。机器探测循环用于在构建板底角处设置工作坐标系,并完成铣削刀具路径以产生所需的六边形几何形状;见图2(c)。
最后,将六边形倒置并切削掉多余的构建板材料以获得最终的六边形尺寸;见图2(d)。第二个虎钳设置中的倒置和加工步骤促使原点位置位于第一个设置的构建板底部。翻转时,原点位于零件的顶部,可以使用机器探测循环方便地识别原点,以设置新的工作坐标系。铣削的主轴转速为5,115 RPM,粗加工进给率为3,302 mm/min,精加工进给率为1,397mm/min。使用攻丝测试和相应的稳定性图来选择这些条件,以选择稳定的主轴速度-切削深度组合(例如,不出现颤振),使用了冷却剂。
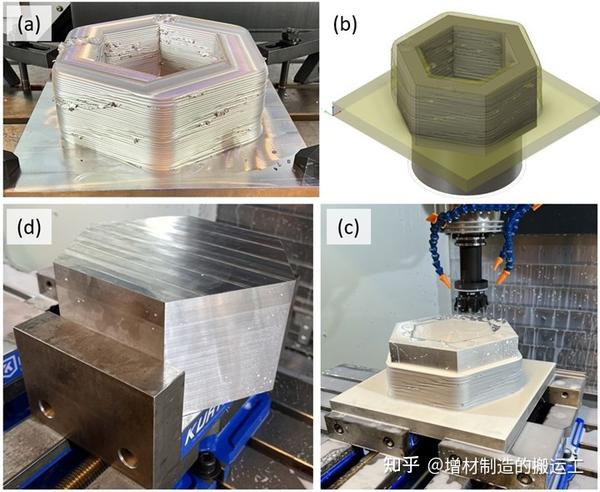
图 2:(a) AFSD后的六边形预制件。(b)扫描和零件设计的对齐。两个坐标系的原点都是构建板角,以便使用探针在CNC铣床上进行方便识别。(c)使用两台虎钳装置铣削预成型件。(d)使用第二台虎钳装置移除构建板,其中零件被倒置并使用相对的六边形表面夹紧。在整个生产过程中保持相同的起源。
照片来源:托尼·施密茨
六边形完成后,其底座(原始构建板的底部)将用作圆柱体的构建平台。AFSD刀具路径规划的原点设置在六边形构建板表面的中心,因此使用L3主轴和寻边器在机器上识别该位置。使用螺旋插补完成沉积,生成层高为2毫米的圆柱体形状。使用275 RPM的主轴速度、139.7毫米/分钟的材料进给速率和132.1毫米/分钟的工具进给速率来沉积初始层。随后的各层以115 RPM的速度以相同的进给速率沉积。
圆柱体预成型件如图3(a)所示,相应的扫描结果如图3(b)所示。通过在六边形基座中心表面设置扫描(作为CAM毛坯模型)、设计和刀具路径坐标系,车床装夹要求只需将零件中心定位在主轴中心线上即可。
这是通过使用车床的三爪卡盘夹紧六角形的三个内表面来完成的。该设置如图3(c)所示,成品部件如图3(d) 所示。六角形基面接触后完成端面、车削和镗孔操作。操作参数为243.84 m/min切削速度、0.89 mm粗加工切削深度、0.25 mm/转粗加工进给速度、0.13 mm精加工切削深度和0.051 mm/转精加工进给速度。硬质合金刀片刀尖半径为0.40毫米。
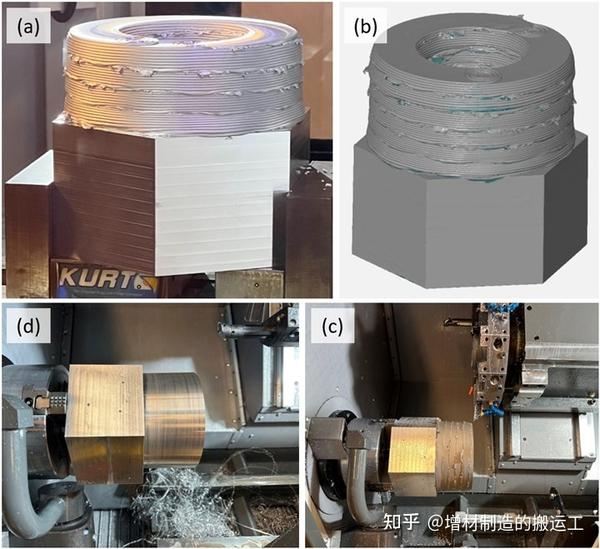
图 3:(a) 六边形底座上的圆柱预成型件。(b) 圆柱沉积后零件的扫描。(c) 使用三爪卡盘将零件夹紧在车床上的六角形内表面上。(d) 从车床上卸下之前的成品零件。照片来源:托尼·施密茨
本部分演示了混合制造场景中AFSD、车削、铣削和结构光扫描的组合。结构光扫描用于生成用于刀具路径生成的毛坯模型,该模型包含可以在加工系统上物理实现的坐标系。六边形圆柱体的几何形状是通过间歇沉积和机加工操作制造的。双面部件的坐标系(沉积在原始构建板的两个表面上完成)使用结构光扫描和原点进行连接,可以使用标准探测例程在加工系统上识别原点。车削和铣削操作均用于生产最终的几何形状和表面光洁度。